Fertigungstechnik der Optik
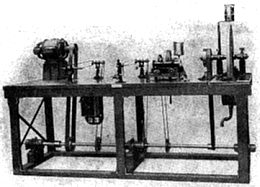
Maschineneinrichtung einer um 1920 modernen Optikerwerkstätte. Von links nach rechts sind folgende Geräte erkennbar:
- Ganz links der Betriebsmotor
- Neben dem Motor ein Polierkopf für Polierscheiben aus Filz, Wolle oder Schmiergel
- In der Mitte die Glasbohrmaschine
- Automatische Facettiermaschine
- Ganz rechts ein Schleifstein
Die Fertigungstechnik der Optik umfaßt die Herstellung von optischen Bauelementen wie Linsen,
Spiegeln,
Prismen und auch kompletten
Optikgruppen, z. B. zusammengesetzte Objektive.
Mit Feinoptik wird das Teilgebiet der Fertigungstechnik der Optik bezeichnet, das die Herstellung hochwertiger Optik umfaßt, wobei die Flächenfehler innerhalb
weniger Wellenlängen des sichtbaren Lichtes liegen und interferenzielle Flächenprüfung wie z. B.
Probeglasprüfung angewandt wird.
Bedingt durch die Eigenart der verwendeten Werkstoffe, die besonderen Werkstückformen und vor allen Dingen wegen der oft ungewöhnlich hohen Anforderungen an die Flächengenauigkeit weichen die Fertigungsverfahren in vielen Punkten von den sonst gebräuchlichen Verfahren ab. Zur Verdeutlichung des Umfanges und der Problematik des Arbeitsgebietes wird daran erinnert, daß z.B. die Frontlinse eines Mikroskopobjektivs kleiner als 1 mm im Durchmesser sein und das Gewicht bei 1 mg liegen kann. Dagegen werden für große Spiegelteleskope Objektivspiegel von mehreren Metern Durchmesser und mehreren Tonnen Gewicht hergestellt. (Der Spiegel des Palomarteleskops hat 5 m. Durchmesser und wiegt etwa l0 Tonnen.) Das Gewicht der Werkstücke kann sich mithin um Zehnerpotenzen unterscheiden. Extrem wie die vorkommenden Größenunterschiede sind auch die Ansprüche, die an die Einhaltung der genauen Flächenform gestellt werden. So sollen bei einem Teleskopspiegel, selbst wenn er mehrere Meter Durchmesser hat, die Abweichungen von der vorgeschriebenen Flächenform unter 0,1 μm bleiben. Das heißt, wenn man den Meridianschnitt des Spiegels betrachtet, so muß dieser auf seiner ganzen Länge, die in der Größenordnung von Metern liegt, auf etwa 1/500 bis 1/1000 der Stärke eines Menschenhaares mit der geforderten Kurve übereinstimmen!
In überwiegender Mehrzahl werden als optisch wirksame Begrenzungsflächen Kugelflächen, und Planflächen verwendet, weil diese bei der Fertigung große Vorteile
bieten. Es gibt aber auch eine Reihe Fälle, bei denen man auf asphärische, d.h. nichtkugelige Flächen, angewiesen ist. Die Herstellung genauer asphärischer
Flächen gehört zu den schwierigsten Problemen der technischen Optik.
Wird ein Körper von zwei oder mehr optisch wirksamen Planflächen begrenzt, so bezeichnet man ihn als Prisma.
Bei der Anfertigung von Prismen sind nicht nur genaue Oberflächen herzustellen, sondern die Flächen müssen auch unter
bestimmten Winkeln zueinander stehen. Die
Toleranzen für die Winkelabweichungen sind ebenfalls oft recht klein. Sie liegen z. B. bei rechtwinkligen Feldstecherprismen bei einigen
Winkelminuten, bei
Dachkantprismen bei etwa 10 Winkelsekunden,
aber es treten auch Fälle auf, wo die Winkel noch genauer eingehalten werden müssen.
Werkstoffe
Wichtigster Werkstoff ist optisches Glas, welches hinsichtlich seiner optischen
Eigenschaften (Brechzahl, Farbenzerstreuung) in großer Mannigfaltigkeit hergestellt wird.
Die Lieferung erfolgt in Form von Plattenglas, Rundscheiben, Preßlingen oder Senkungen. Außer Glas finden
Quarzglas und Kristalle
wie Quarz,
Steinsalz, Lithiumfluorid, Kalkspat u.a. Anwendung, wenn besondere Eigenschaften wie gute Durchlässigkeit im UV bzw. IR gefordert werden oder Optiken für
Polarisationszwecke herzustellen sind.
Fertigungsstufen
Jedes Werkstück durchläuft bis zu seiner Fertigstellung eine Reihe von Arbeitsstufen. Die ersten beiden Arbeitsstufen haben die rohe und feinere Formgebung zum
Ziel.[vergl Formgebung] Beim darauffolgenden Feinschleifen
werden die zu polierenden Oberflächen so weit verfeinert, daß die Abweichung von der geforderten Flächenform und die Rauhtiefe (Mikrostruktur der Oberfläche)
einige μm nicht überschreitet.
Die feingeschliffenen Flächen werden in einem weiteren Arbeitsgang poliert, wobei sie nicht nur blank und durchsichtig werden, sondern auch innerhalb der
gegebenen Toleranzen ihre vorgeschriebene Flächenform erhalten müssen. Es folgen je nach Art des Werkstücks einige Nacharbeiten wie Anschleifen von Fasen,
Zentrieren (bei Linsen), Säubern, Kontrolle auf Fertigungs- und Werkstoffehler; gegebenenfalls folgen noch Oberflächenbehandlungen, wie Verspiegeln oder
Aufbringen reflexmindernder Schichten. Sind zwei oder mehrere Teile mit ihren optisch wirksamen Flächen fest zu verbinden, so erfolgt dies durch
Feinkitten
oder Ansprengen. Als abschließender Arbeitsgang sind die fertigen Optikteile in ihre Fassungen einzubauen.
Begriffe
Bevor die einzelnen Arbeitsstufen näher beschrieben werden, ist es zweckmäßig, zwei Begriffe zu erklären, die von den sonst in der Technik gebräuchlichen abweichen.
- Mit Fräsen wird in der Fertigungstechnik der Optik die Bearbeitung von Glas mit gebundenen Schleifmitteln, insbesondere mit Werkzeugen, die mit Diamantkorn bestückt sind, bezeichnet. (In der Metallbearbeitung wird dieser Vorgang mit Schleifen bezeichnet.)
- Mit Schleifen wird die Bearbeitung eines Werkstücks mit losen Schleifmitteln bezeichnet. (In der Metallbearbeitung wird ein nass oder feucht arbeitendes Schleifverfahren mit losem Korn als Läppen bezeichnet).
Für die erste rohe Formgebung sind plastische und mechanische Verfahren gebräuchlich. Zu den plastischen Verfahren gehören das Pressen und das Senken. Beim Pressen wird das über den Einsenkpunkt (Glas) erhitzte Glas unter einer Presse in die gewünschte Form (zuzüglich Bearbeitungsaufmaß) gebracht. Die Presslinge werden danach noch einmal bis zum Umformungspunkt ( Glas) erhitzt und langsam abgekühlt, so daß keine Spannungen mehr auftreten können. Beim Senken wird eine Glasplatte entsprechender Abmessungen auf eine Senkform gelegt, in die sie sich nach Erhitzung über den Einsenkpunkt durch ihr Eigengewicht hineinsenkt.
Zu den mechanischen Verfahren gehören Trennen, Aufteilen, Anreißen und Aufbrechen, Bröckeln, Rundieren, Schruppen und Fräsen. Beim Trennen werden die Glasblöcke mit einer Trennmaschine zerlegt. Die Trennmaschine oder Diamantsäge besteht aus einer meist mit Diamantkorn bestückten Trennscheibe, die wie eine Kreissäge arbeitet (Schnittbreite bei etwa 400 mm Scheibendurchmesser etwa 1,5mm). Als Kühlmittel wird Petroleum bzw. ein Gemisch aus Petroleum und Spindelöl oder auch Sodawasser verwendet. Die Glasblöcke werden von einem Schraubstock gehalten und mit einer Schwinge an die Trennscheibe gepresst (Gewichtzug o. ä.). Die Schnittgeschwindigkeit je dm2 beträgt etwa 5 bis 10 min. Sie hängt von der Glasart und auch von dem Zustand der Trennscheibe ab. Trennmaschinen werden für Sonderaufgaben auch mit einem Trennband nach Art einer Bandsäge gebaut.
Aufteilen, Anreißen und Aufbrechen.
Um dünne Glasscheiben (Schnittglas oder Tafelglas) in kleinere Formte zu zerlegen, wird die Scheibe aufgeteilt, indem sie unter Verwendung von Lineal, Maßstab und Winkel angezeichnet wird (matte Flächen mit Bleistift, blanke Flächen mit Fettstift). Die aufgeteilte Fläche wird mit einem Glasschneider (Schneidrädchen, Schneidrolle, Schneiddiamant) angerissen und dann aufgebrochen, d. h. die durch Kerbwirkung beim Anreißen hervorgerufenen senkrecht in das Glas laufenden Sprünge werden unter Zuhilfenahme eines Hammers vergrößert und die Scheiben an den Schnittstellen auseinandergebrochen
Bröckeln und Rundieren.
Sollen z.B. derart zugerichtete quadratische Glasplättchen zu Rundscheiben verarbeitet werden, so werden sie durch Bröckeln in eine kreisrunde Form gebracht. Dabei wird mit einer Zange, der Bröckelzange, durch Abbrechen oder Abzwicken kleinster Glasteilchen das überflüssige Material entfernt. Die gebröckelten Rundlinge werden rundiert, indem der Rand sauber kreisförmig geschliffen wird. Es werden häufig eine Anzahl Rundlinge zu einer Stange zusammengekittet und gleichzeitig rundiert. Das Rundieren erfolgt entweder durch Abschleifen der zylindrischen Ränder auf einer horizontal rotierenden ebenen Gußscheibe mit losen Schleifmitteln, indem die zusammengekitteten Gläser wie eine Walze abgerollt werden, oder aber die zylindrische Rolle wird auf eine senkrecht rotierende Spindel (Schruppmaschine) gebracht und mit einem einseitig offenen Blechring, dem Rundierblech, mit losen Schleifmitteln abgeschliffen. Zum maschinellen Rundieren verwendet man besondere Rundiermaschinen, die wie die Rundschleifmaschinen in der Metallbearbeitung aufgebaut sind. Die zu einer Stange zusammengekitteten Scheiben erhalten an den Enden Metallplatten mit Senkungen, so daß sie zwischen Spitzen rotieren können, oder sie werden durch Druck zusammengehalten. Das Rundschleifen der Ränder erfolgt durch eine schnell rotierende Stirnscheibe (Schleifscheibe oder Diamantwerkzeug), wobei entweder das Werkzeug oder das Werkstück einen Längsvorschub erhält. Durch eine Begrenzung des Tiefenvorschubs des Werkzeuges wird der Rundiervorgang abgebrochen, wenn das Werkstück den richtigen Durchmesser erhalten hat.
Bei der weiteren Formgebung erhält das Werkstück die vorgesehene Form zuzüglich eines relativ geringen Aufmaßes für die Feinbearbeitung der optisch wirksamen Oberflächen. Dieser Arbeitsgang erfolgt entweder durch Schruppen oder durch Fräsen.
Beim Schruppen wird durch Schleifen auf einer Schruppmaschine mit losen Schleifmitteln für gewöhnlich in Handarbeit dem Werkstück die richtige Form gegeben. Es werden je nach Flächenform ebene, sphärisch-konvexe oder -konkave Werkzeuge benutzt, die auf einer senkrecht gelagerten Spindel schnell rotieren. Das Werkstück wird mit der einen Hand gleichmäßig auf dem Werkzeug hin- und herbewegt und langsam gedreht, während mit der anderen Hand in Wasser aufgerührtes Schleifmittel gröberer Körnung aufgetragen wird. Als Schleifmittel wird hierbei und bei dem nachfolgenden Feinschleifen fast ausschließlich Elek-trokorund oder Siliciumkarbid verwendet in verschiedenen Feinheitsstufen. Diese künstlichen Schleifmittel haben den früher gebräuchlichen Naturkorund (Schmirgel) wegen ihrer Gleichmäßigkeit weitgehend verdrängt. Die Schleifmittel werden durch Schlämmen oder Sieben nach Korngrößen getrennt. Die Klassifizierung kann nach Sinkzeiten in Minuten oder nach Maschenzahl des Siebes in cm2 erfolgen. Die groben Schleifmittel, wie sie z. B. zum Schruppen verwendet werden, haben Korngrößen von etwa 150 bis 250 μm. Zum Feinschleifen werden Korngrößen bis herab zu etwa 5 bis 10 μm verwendet.
Sind größere Stückzahlen herzustellen, so ist die maschinelle Bearbeitung durch Fräsen rationeller als das Schruppen von Hand. Beim Fräsen. werden die Werkstücke mit gebundenen Schleifmitteln meist mit Werkzeugen mit Diamantkorn bearbeitet. Die Diamantwerkzeuge tragen einen Besatz aus Diainantkorn, welches durch Mörsern in einem Stahlmörser hergestellt wird und wie die anderen Schleifmittel nach Korngröße abgestuft ist. Die Bezeichnung der Diamantkorngrößen erfolgt nach DIN 848 (Empfehlung). In dieser Empfehlung bedeutet D Diamant, die anschließende Zahl mittlere Korngröße in izm. Für den Einsatz von Diamantkörnungen zum Zwecke der Glasbearbeitung k'ann unterschieden werden in feine Körnung, Bereich von etw9 D 7 bis D 30, mittlere Körnung, Bereich von etwa D 50 bis D 150, und grobe Körnung über D 150 bis D 250.
Das Diamantkorn wird mit einem Bindemittel durch Sintern, Pressen oder Walzen auf das Werkzeug aufgebracht. Die Bindung kann aus Metall (Bronze, Stahl, Hartmetall), aber auch aus Kunststoff bestehen. Die Diamantwerkzeuge arbeiten mit hohen Umdrehungszahlen (Umfangsgeschwindigkeit etwa 25m/s).
Werkzeuge
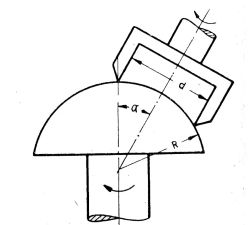
Die Bearbeitung optisch wirksamer Oberflächen (Planflächen, sphärische und asphärische
Rotationsflächen, torische Flächen) erfolgt entweder mit Stirnfräsern oder
mit Topf Werkzeugen. Die letztgenannte
Werkzeugform findet für die Bearbeitung sphärischer Flächen heute eine ausgedehnte Anwendung. Sie wird sowohl für die Bearbeitung von Einzellinsen als auch von
Linsenkörpem benutzt. Das Verfahren beruht
auf der Überlegung, daß ein zylindrisches Werkzeug mit seiner ganzen kreisförmigen Arbeitskante alle Kugelflächen berühren kann, deren Radius den Arbeitsradius
des Werkzeuges übersteigt. Die Maschinen,
die nach diesen Gesichtspunkten gebaut sind, besitzen zwei Spindeln, die in einer Ebene gelagert sind, jedoch in einem veränderlichen Winkel zueinander stehen.
Der Arbeitsdurchrnesscr d des Werkzeuges und
der Winkel α, unter dem die beiden Achsen zueinander stehen, bestimmt den Radius R des Werkstücks: R=d/2 sinα (Abb. rechts). Durch die Veränderung des
Einstellwinkels ist man mithin in der Lage, mit einem
einzigen Werkzeug einen großen Radienbereich zu überdecken. Damit die ganze Fläche des Werkstücks bearbeitet wird, ist es erforderlich, daß die Arbeitskante des
Werkzeugs durch den Punkt geht, in dem die
Rotationsachse des Werkstücks dessen Oberfläche schneidet.
Andernfalls würde in der Mitte des Werkstücks ein Teil unbearbeitet bleiben. Ferner muß das Werkzeug
so groß sein, daß es den Rand des Werkstücks
bedeckt oder darüber hinausragt.
Der mechanische Aufbau der Maschinen und die Lagerung der Spindeln, insbes. der schnell-rotierenden Arbeitsspindel, muß hohen Anforderungen genügen. Mit
Topfwerkzeugen können sowohl Konvex- als auch
Konkavflächen gefräst werden. Im Grenzfall der Planfläche verlaufen die beiden Achsen parallel. Die Bearbeitungsverfahren mit Stirnfräsern sind gegenüber den
geschilderten Verfahren mit Topfwerkzeug
benachteiligt, weil bei ihnen die Abtragung nur in Punktberührung erfolgt, während die Topfwerkzeuge in Linienberührung arbeiten. Beim Fräsen von Kugelflächen
wird das schnellrotierende
Werkzeug auf einer Kreisbahn um den Punkt geschwenkt, der dem Krümmungsmittelpunkt der zu erzeugenden Kugelfläche entspricht und der auf der Rotationsachse des
Werkstücks liegt (Abb. 4).
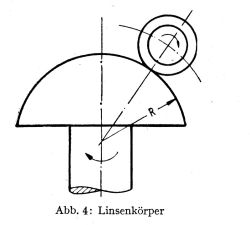
Wichtiger ist die Anwendung von Stirnwerkzeugen für die Vorbearbeitung von torischen Flächen (für Brillengläser) und von asphärischen Rotationsflächen. Bei torischen Flächen wird das Werkzeug wie bei Kugelflächen auf einer Kreisbahn geführt, während die Werkstücke auf einem Ring angebracht sind, der langsam rotiert. Für asphärische Rotationsflächen benutzt man Kopierfräsmaschinen. Das Werkzeug wird durch eine Kurve, die oft im Maßstab 1: 1 der Meridiankurve der Asphäre entspricht, gesteuert.
Linsenkörper.
Die durch Schruppen oder Fräsen vorgearbeiteten Werkstücke werden fein geschliffen und poliert. Für diese Arbeitsgänge werden, sofern es möglich ist, eine mehr
oder weniger große Zahl Werkstücke zu einem
Körper vereinigt. Linsen werden zu diesem Zweck durch Kitten auf einem Linsentragkörper befestigt. Sie erhalten auf der Rückseite einen Klotz aus Kittpech oder
Siegellack. Mit den zu
bearbeitenden Flächen werden sie dann in eine Aufsetzschale eingerieben, die fast den gleichen Radius hat wie die erste Feinschleifschale. Ein angewärmter
Tragkörper wird auf die Kittklötzchen gedrückt und
damit die Linsen auf dem Tragkörper angekittet. Bei großen Serien werden auch Linsentragkörper verwendet, die für jede Linse eine besondere Einfräsung haben,
wobei die Linse am Rand fest aufliegt. Diese
Tragkörper gewährleisten eine bessere Einhaltung der Mittendicke.
Die Zahl der Linsen, die auf einem Tragkörper vereinigt werden können, hängt vom Radius der zu bearbeitenden Fläche und vom Durchmesser der
Linsen ab. Die Körper werden nicht ganz bis zur Halbkugel besetzt, da sich Halbkugeln nicht gut
bearbeiten lassen.
Das Aufkitten oder Zusammenkitten von Werkstücken für die Bearbeitung bezeichnet man als Rohkitten. (Im Gegensatz zum Feinkitten, bei dem optisch-wirksame Flächen
von fertigen Linsen oder Prismen mit
Kanadabalsam oder einem anderen Feinkitt miteinander verkittet werden). Beim Rohkitten ist zu beachten, daß die aufzukittenden Teile sich nicht durch die
unterschiedliche Ausdehnung von Werkstoff, Kitt und
Linsenkörper verziehen dürfen. Bei der Bearbeitung müssen die Linsen gut festsitzen, sie dürfen sich auch nicht, wenn beim Polieren eine Erwärmung erfolgt,
verschieben. Die Eigenschaften des Rohkittes
werden oft so abgestimmt (z. B. bei der Massenfertigung von Brillengläsern), daß, wenn nach fertiger Politur die noch warmen Körper unter kaltes Wasser gebracht
werden (abgeschreckt werden), die Gläser
sauber vom Kitt abplatzen. Dadurch wird der Arbeitsaufwand für die Reinigung der Flächen stark reduziert.
Prismenkörper.
Auch in der Prismenfertigung wird häufig eine Anzahl Prismen zur gleichzeitigen Bearbeitung einer Fläche zu einem Prismenkörper vereinigt. Die hierbei
anzuwendende Technologie hängt im wesentlichen von der
geforderten Genauigkeit ab, mit der die Fläche zu bearbeiten ist, und von den zulässigen Winkeltoleranzen, aber auch von der herzustellenden Stückzahl.
Die einfachste und billigste Art des Prismenkörpers ist der Gipskörper. Die Prismen werden mit den zu bearbeitenden Flächen auf eine gute Planfläche aufgesetzt
oder mit weichem Kitt aufgekittet.
Über die Prismen wird ein Gipskörper gestülpt. Dieser besteht aus einer runden Grundplatte mit Spindelanschlußgewinde für die Schleif- und Poliermaschinen und aus
einem Rand, der fest sein kann oder auch
durch einen Verschluß von der Grundplatte gelöst werden kann. Die Form wird mit Gipsbrei gefüllt. Nach dem Abbinden des Gipses werden die Prismen von der
Planplatte abgezogen (evtl. nach Anwärmen).
Die zu bearbeitenden Prismenflächen müssen etwa 1 bis 2 mm über den Gips vorstehen und sind entsprechend
freizulegen. Die Gipsoberfläche muß durch
einen Lacküberzug gegen das Eindringen von Feuchtigkeit geschützt werden. Durch das Abbinden des Gipses erfahren die Prismen im allgemeinen kleine Lageänderungen,
die Winkelfehler hervorrufen. Gipskörper
sind nur dort verwendbar, wo die Winkeltoleran zen in der Größenordnung von Bogenminuten a liegen. Für größere Serien werden auch Metallprismenkörper verwendet
mit genau im Winkel gearbeiteten
Ausfräsungen, in die die Prismen eingekittet werden. Werden sehr hohe Anforderungen an die Winkelgenauigkeit gestellt, wie i z. B. bei Dachkantprismen, so sind
Ansprengkörper zu verwenden.
Die Prismen werden mit einer fertigen Planfläche an sehr genau gearbeitete Hilfsstücke angesprengt, die wiederum auf eine große Planplatte angesprengt werden.
Bei der Bearbeitung wird die Parallelität der
bearbeiteten Flächen zur Grundfläche optisch kontrolliert. Bei kleinen Stückzahlen benutzt man auch quadratische Glaskörper (Ansprengklötze), an deren genau im
Winkel gearbeitete Seiten die Prismen
angesprengt werden.
Schleifen
Schleifen ist das älteste, aber auch aufwändigste Verfahren, Glaslinsen herzustellen. Schon mehrere Jahrzehnte gibt es auch für asphärischen Oberflächen Linsen entsprechende Maschinen, aber bis zur Serienreife von Abformverfahren waren sie auf besonders hochwertige und teure Objektive beschränkt. Seit dem Jahr 2000 hat sich die Maschinentechnik auf Basis von CNC-Steuerungen soweit weiterentwickelt, dass gegenwärtig der Einsatz von CNC-Maschinen zur Fertigung von Asphären gängige Praxis ist. Die CNC-Bearbeitung ermöglicht vor allem auch die Bearbeitung von Quarzen oder von Optiken mit großen Durchmessern, die mittels Abformung gar nicht oder nicht in der benötigten Güte hergestellt werden können. Sie kommen hauptsächlich in den Bereichen Messtechnik, Medizintechnik, Lasertechnik sowie in der Luft- und Raumfahrt zum Einsatz.
Geschruppte, vorgeschliffene oder gefräste Flächen müssen vor dem Polieren fein geschliffen werden. Dieser Arbeitsgang hat die Aufgabe, einerseits die
Mikrostruktur der Flächen so weit zu verfeinern,
daß die Rauhtiefe nur noch in der Größenordnung von einigen μm liegt, zum anderen aber auch die Abweichungen von der Flächenform (im großen gesehen) auf einige
μm zu reduzieren. Der Feinschleifprozeß
wird in mehreren Stufen mit verschieden feinen Schleifmittelsorten durchgeführt (beispielsweise mit drei verschiedenen Körnungen mit
Korngrößen von etwa 65 μm;
45 μm und 15-20 μm.
Mit jeder Körnung wird so lange geschliffen, bis die letzten Spuren des vorhergehenden Schliffs verschwunden sind. In der Praxis ist es oft erforderlich, für jede
Feinschleifstufe ein anderes Werkzeug zu
verwenden. Das gilt besonders für die Bearbeitung von Linsenkörpern, die stärker gekrümmt sind, d. h., der Halbkugel nahekommen. Die Radien der verschiedenen
Schleifwerkzeuge sind so abzustimmen, daß die
beim Schleifen erfolgende Abtragung berücksichtigt wird. Bei der Bearbeitung von Konvexflächen hat das nächstfolgende Schleifwerkzeug jeweils einen um den
Betrag der Abtragung verminderten Radius. Der
Radius der letzten Feinschleifstufe stimmt fast genau mit dem geforderten Linsenradius überein (bei der Bearbeitung von Konkavflächen werden die Radien der
Schleifwerkzeuge von Stufe zu Stufe größer).
Das Werkstück wird in beiden Fällen vom Rande her zuerst angegriffen, und der, Schleifprozeß wird so lange fortgesetzt, bis auch die Mitte des Werkstücks
"durchgeschliffen" ist, d.h., die Schleifspuren
der vorhergehenden Stufe verschwunden sind.
Schleifwerkzeuge.
Die Schleifwerkzeuge werden aus Grauguß oder Messing hergestellt und sind häufig von annähernd gleicher Größe wie das Werkstück. Für die Arbeit auf Hebelmaschinen haben Konvexwerkzeuge (Schleifköpfe) ein Anschlußgewinde zum Aufschrauben auf die Spindel. Konkavwerkzeuge (Schleifschalen) haben ebenfalls einen Zapfen mit Anschlußgewinde, in das eine Kugelpfanne eingeschraubt wird, in die der Kugelstift des Hebels bei oben laufender Schleifschale eingreift.
Polieren.
Die feingeschliffenen Flächen müssen noch poliert werden. Ziel des Polierens ist eine blanke Oberfläche ohne jede Schleifspuren, die gleichzeitig in bezug auf
Flächenform und Genauigkeit den gestellten
Forderungen entspricht. Der Polierprozeß unterscheidet sich in wesentlichen Punkten vom Schleifprozeß. Während das Schleifen in erster Linie als mechanischer
Abtragevorgang zu betrachten ist, spielen beim
Polierprozeß auch chemische Reaktionen eine wichtige Rolle. Hieran ist nicht nur das
eigentliche Poliermittel wie
Polierrot Fe2O3 oder
Ceroxid, sondern auch das Polierpech bzw. der Polierfilz sowie das Wasser
beteiligt.
Zum Polieren werden im Gegensatz zum Schleifen die Polierschalen mit einem weichen Mittel ausgekleidet. Hierfür wird in der Feinoptik, wo mit Interferenzen
(Probeglas) geprüft wird, fast ausschließlich
Pech verwendet. Bei der Herstellung von Optik mit geringeren Genauigkeitsforderungen, z. B. Kondensoren, Brillengläsern usw., benutzt man Filz, weil hiermit eine
schnellere Politur erzielt wird.
Schleif- und Poliermaschinen.
Zum Feinschleifen und zum Polieren werden die gleichen Maschinentypen benutzt. Für Mikrooptik und kleinere Einzellinsen sind die sog. Tretbänke gebräuchlich. Bei den Tretbänken läuft in einem Becken eine kleine vertikal stehende Spindel, die das Werkzeug trägt. Der Antrieb erfolgt durch zwei Fußpedale. Das Werkstück wird an einem Futter befestigt und von Hand bewegt. Ähnliche Maschinen jedoch mit Motorantrieb werden auch für Handarbeit benutzt. Die wichtigste Rolle spielen in der Feinoptik die Hebelmaschinen. Auch bei diesen Maschinen läuft die vertikal stehende Arbeitsspindel in einem Becken und trägt das Werkstück oder das Werkzeug. Die zweite oben laufende Komponente wird durch einen Hebel mit Kugelstift bewegt. Sie wird jedoch in ihrer Bewegung durch den auf der Arbeitsspindel rotierenden Teil geführt. Da man nur Kugelflächen mit gleichen Radien so gegeneinander verschieben kann, daß sich die Flächen stets in allen Punkten berühren, gleichen sich bei diesem Verfahren die Fehler der Flächen gegenseitig aus. Die Genauigkeit der Flächen hängt dabei nicht mehr von irgendwelchen mechanischen Führungen ab. Das obere Teil wird durch Reibung mit in Rotation versetzt, bleibt jedoch in der Drehzahl etwas hinter dem unteren zurück. Der Antrieb des Hebels erfolgt bei den meisten Hebelmaschinen über einen Exzenter. Der Hebelausschlag läßt sich nach Bedarf verändern. Desgleichen läßt sich die Lage der Bahn, die der Kugelstift (d. h. die Mitte des oberen Teiles) beschreibt, verändern. Der Kugelstift kann z.B. über die Mitte der unteren Fläche fahren oder aber über einen seitlichen Teil der Fläche. Die Spindeldrehzahl sowie auch das Verhältnis von Spindeldrehzahl zu Hebelausschlägen wird nicht nur durch Form und Größe des Werkstücks bestimmt, sondern auch durch die zu erzielende Genauigkeit. Bei stark gekrümmten Flächen läßt man häufig die Arbeitsspindel schneller laufen als den Hebel, während es bei Planflächen oder schwach gekrümmten Flächen oft günstiger ist, wenn auf eine Spindeldrehung mehrere Hebelausschläge kommen. Bei genauen Flächen, die grundsätzlich Pechpolitur erhalten, wird mit wesentlich geringeren Drehzahlen gearbeitet als bei Filzpolitur.
Für Filzpolitur wurden auch z. B. in der Brillenglasindustrie Maschinen entwickelt, bei denen anstelle eines Hebels ein Kurbeltrieb verwendet wird. Bei diesen Hängespindeln beschreibt die Mitte des oberen Werkstücks einen Kreis, dessen Radius in gewissen Grenzen zu verstellen ist.
Für sehr große astronomische Flächen wurden von den verschiedenen Herstellern Sondermaschinen entwickelt, die zwar im Prinzip den Hebelmaschinen entsprechen, aber den besonderen Erfordernissen angepaßt sind. Maschinen für große Teleskopspiegel werden z.B. zweckmäßigerweise so konstruiert, daß der Spiegel zum Prüfen nicht von der Maschine abgehoben werden braucht, sondern mitsamt seiner Aufnahme und der Spindel durch Kippung aufgerichtet werden kann.
Für torische Flächen bei Brillengläsern werden Maschinen benutzt, bei denen die Gläser auf einem Ring angeordnet sind, der um eine Achse rotiert (Tori-Ringmaschinen). Bei torischen Konvexflächen befinden sich die Gläser auf der Außenseite des Ringes, bei Konkavflächen auf der Innenseite. Zum Schleifen und Polieren werden Werkzeuge mit einer torischen Oberfläche benutzt, d. h., die Oberfläche hat in zwei senkrecht aufeinanderstellenden Schnitten verschiedene Radien. Der Radius in dem einen Hauptschnitt wird durch den Ringhalbmesser bestimmt, d. h. durch den Abstand, den die zu bearbeitenden Glasoberflächen von der Rotationsachse des Ringes haben. Der Radius im anderen Hauptschnitt wird nur durch das Werkzeug bestimmt. Die Werkzeuge sind freibeweglich angebracht und werden durch Federkraft angepreßt. Sie erhalten durch ein Hebelsystem eine Bewegung senkrecht zur Rotationsrichtung der Gläser. Diese Bewegung darf nicht zu groß gewählt werden, da sonst eine Flächenberührung nicht mehr gewährleistet ist.
Für den Einschliff der Nahteile in Zweistärkengläser werden Maschinen benutzt, die ähnlich wie die Fräsmaschinen mit Topfwerkzeug mit einem zylindrischen Werkzeug arbeiten, dessen Rotationsachse zur Rotationsachse des Werkstückes um einen bestimmten Winkel geneigt ist.
Abformung
Dieses für Serienfertigung kostengünstige Verfahren wird häufig für Kamera-, Kondensorlinsen sowie für Laser-Pick-Up-Optiken eingesetzt.
- Asphärische Linsen aus Kunststoff können durch Abformen sehr preisgünstig hergestellt werden. Für Fotoobjektive ist jedoch ihre Formgenauigkeit und Konstanz ihrer Eigenschaften nicht gut genug.
- Man kann auf eine sphärische Glaslinse eine Kunststoffschicht mit asphärischer Oberfläche aufpressen. Die Qualität eines solchen Elements ist für Fotoobjektive mittlerer Güte ausreichend.
- Für hochwertige Fotoobjektive wird eine Glaslinse direkt mit einer abgeformten asphärischen Oberfläche hergestellt (Blankpressen). Man braucht dafür aber geeignete Gläser mit nicht zu hoher Transformationstemperatur, denn das Material der Pressstempel ist nur begrenzt temperaturbeständig. Man kann somit nicht jedes optische Glasverwenden.
Zentrieren.
Linsen für Objektive usw. werden nach der Bearbeitung der optischen Flächen zentriert, damit die optische Achse, deren Lage durch die Gerade durch die beiden Krümmungs-Mittelpunkte gekennzeichnet ist, auch durch die geometrische Mitte der Linse geht. Die Linse wird zu diesem Zweck auf das Futter einer horizontal rotierenden Spindel einer Zentriermaschine gekittet und so ausgerichtet, daß die beiden Krümmungsmittelpunkte mit der Rotationsachse zusammenfallen. Das wird entweder optisch kontrolliert (die Spiegelbilder müssen bei laufender Spindel stillstehen) oder mechanisch geprüft (Messung des Taumelschlages). Das Abschleifen des zylindrischen Linsenrandes erfolgt entweder durch eine Metallplatte bzw. auch ein Blech mit losen Schleifmitteln oder durch eine Schleifscheibe (evtl. auch Diamanwerkzeug). Wo größere Serien von Linsen zu zentrieren sind, werden Zentrierautomaten benutzt, bei denen das Schleifwerkzeug einen automatischen Vorschub erhält, bis der eingestellte Durchmesser erreicht ist. Das Auf kitten der Linsen auf ein laufendes Futter kann bei stärker gekrümmten Linsen vermieden werden durch ein Spannverfahren, bei dem sich die Linse zwischen zwei Glocken selbsttätig zentriert.
Feinkitten.
Sind zwei oder mehr Teile mit ihren optisch wirksamen Flächen fest miteinander zu verbinden, so erfolgt dies durch Feinkitten oder Ansprengen. Beim Feinkitten werden die Linsen durch eine dünne Kittschicht, deren Brechzahl mit der der zu verwendenden Gläser etwa übereinstimmt, verbunden. Als wichtigster Optikkitt findet Kanadabalsam Anwendung. Der Kitt wird in erwärmtem Zustand zwischen die ebenfalls erwärmten Flächen gebracht und unter Vermeidung von Lufteinschlüssen zu einer sehr dünnen Schicht ausgedrückt. Er wird bei Abkühlung durch Erstarren fest.
Ansprengen.
Hochwertige Flächen kann man unter Vermeidung einer Kittschicht ansprengen. Die Flächen, die sehr genau zusammenpassen müssen, werden in sorgfältig gereinigtem Zustand zusammengebracht, bis die Interferenzfarben zwischen den Flächen ganz verschwinden und die beiden Teile durch Adhäsion fest aneinander haften (man sagt auch, die Flächen befinden sich in optischem Kontakt).
Ein weiterer Arbeitsgang ist das Aulbringen reflexmindernder oder reflektierender Schichten (Vergütung bzw. Verspiegelung): -> Schichten, dünne.
Prüf- und Meßverfahren.
Alle feinoptischen Arbeitsstufen müssen exakten Kontrollen und Messungen unterliegen, wenn ein befriedigendes Ergebnis erzielt werden soll. Die Prüf- und Meßverfahren können in nachstehende Gruppen eingeteilt werden:
- 1) Werkstoffprüfungen:
- Messung der Brechzahl und der Dispersion
- Brechzahlbestimmung
- Dispersion
- Spektrometer, Refraktometer
- Prüfung auf Schlieren (Schlierenmethode)
- Prüfung auf Spannungen (Spannungsprüfer)
- Messung der Brechzahl und der Dispersion
- 2) Prüfung und Messung optischer Oberflächen:
- Prüfung mit Probeglas (- Probeglas, - Newtonsche Ringe);
- Radienmessung (- Sphärometer);
- Ebenheitsprüfung (- Interferometer, - Interferenzstreifen gleicher Dicke); Prüfung auf Schleif- und Polierfehler wie Kratzer, Wischer und Schleifgrübchen.
- 3) Winkelmessungen (- Goniometer, - Spektrometer, Autokollimations-Fernrohr). Hierher gehört auch die Prüfung von planparallelen Platten, d. h. die Messung des Keilfehlers geometrisch-optisch (Autokollimations-Fernrohr) oder interferentiell (Fizeausche Streifen, Haidingersche Ringe).
- 4) Messung von Längen, Linsendicken, Durchmessern, Abständen usw.
Als Hilfsmittel werden benutzt: Maßstab, Schiebelehre, Zehnteltaster, Mikrometerschraube, Meßuhrdickenmesser, Optimeter, Längenmesser u. ä. - 5) Messung und Prüfung des Korrektionszustandes optischer Systeme, - Objektivprüfung.

© biancahoegel.de;
Datum der letzten Änderung: Jena, den: 10.11. 2023