Halbschalenbauweise
.png)
3: Schalenbauweise,
4: Halbschalenbauweise
Mit Halbschalenbauweise (englisch stressed skin oder semi-monocoque) wird im Flugzeugbau eine Konstruktionsweise zum Aufbau von Flugzeug- und Raketenrümpfen, seltener auch von Tragflächen bezeichnet, bei der die „Stärke“ der Außenhaut (Beplankung) dieser Bauteile so bemessen ist, dass sie einen Großteil der auftretenden Kräfte aufnehmen kann. Gegenüber der reinen Schalenbauweise (Monocoque), die ohne innere Verstärkungen oder mit geringen Aussteifungen durch Querspanten auskommt, verwendet die Halbschalenbauweise zusätzlich auch Längsaussteifungen. Dies sind typischerweise Longerons (Rumpfholme) und Stringer (schwächere Longerons), die zur Entlastung der Außenhaut beitragen. Damit soll die Hauptschwäche der reinen Monocoquebauweise, nämlich eine ausreichende Festigkeit bei möglichst geringem Gewicht zu erreichen, behoben werden. Eine konsistente Unterscheidung der Begriffe Schalen- und Halbschalenbauweise ist in der Literatur jedoch nicht zu erkennen. Oft werden beide Bezeichnungen synonym verwendet.
Geschichte
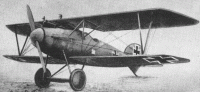
Die erste nachgewiesene Anwendung der Monocoque-Bauweise wurde 1911 auf der Olympia-Aero-Show mit einer von Handley-Page entworfenen Maschine präsentiert. Die Rumpfschale der Type D (rückwirkend 1924 als H.P.4 bezeichnet) bestand vornehmlich aus Mahagoni-Holz. Weitere frühe Anwendungen der Schalenbauweise im Luftfahrzeugbau sind die Deperdussin Monocoque Racer aus dem Jahr 1912, als weiteres Beispiel für die anfänglich verwendete Holzbauweise. Der Rumpf der von Jack Northrop konstruierten Loughead S-1 aus dem Jahr 1919 wurde in zwei Betonformen hergestellt. Hier war der Rumpf aus mehreren Lagen Sperrholz aufgebaut. In Deutschland waren typische Beispiele die Albatros D.V aus der Zeit des Ersten Weltkriegs und die später gebaute Heinkel He 70.
Erste Versuche mit einer Ganzmetall-Schalenbauweise unternahm Dornier 1917 mit der Dornier Cl.I, bei der die Holz-Schalenkonstruktion der Albatros-Doppelsitzer in den Metallbau übertragen werden sollte. Inwieweit die Rumpfhülle wirklich dazu geeignet war Kräfte aufzunehmen, ist jedoch ungeklärt. Die ersten tatsächlich in einer Ganzmetall-Schalenbauweise ausgeführten Flugzeuge waren die erstmals im Juni 1918 geflogene Dornier-Zeppelin D.I und die im Juli 1920 auf der Olympia Airshow gezeigte Short Silver Streak.
Konstruktive Ausführung
Allgemeines
Bei der Halbschalenbauweise wird zur Verstärkung der Außenhaut und zur Wahrung der Querschnittsform gewöhnlich eine Unterstruktur eingesetzt, die sich aus Longerons, Stringer, Spanten/Schotten und Formern zusammensetzen kann. Auf den Rumpf wirkende Biegekräfte werden von Longerons aufgenommen, die parallel zur Rumpflängsrichtung laufen. Stringer haben einen kleineren Querschnitt gegenüber Longerons und unterstützen diese bei der Aufnahme von Druckkräften und erhöhen die Steifigkeit des Rumpfs. Formspanten und Schotten dienen vornehmlich zur Erhaltung der Querschnittsform und erhöhen die Stabilität der Stringer gegen Knicken. Schotten werden bevorzugt dort eingesetzt, wo Kräfte konzentriert in den Rumpf oder die Tragflächen eingeleitet werden. Dies sind z. B. Triebwerksaufhängungen, Tragflächenanschlüsse, der Fahrwerksanschlag und die Anschlüsse der Leitwerksflossen. Das Einteilen in Spanten und Stringer wird im Fachbegriff auch „Straken“ genannt.
Neben der Ausnutzung des hohen Widerstandsmoments von geschlossenen kreisähnlichen Rumpfquerschnitten, ist der Hauptvorteil der Schalen- bzw. Halbschalenbauweise gegenüber dem Fachwerkrumpf die Möglichkeit eine aerodynamisch ausgebildete Rumpfform zu erreichen, ohne zusätzliche formgebende Bauteile einsetzen zu müssen. Hinzu kommt, dass der Innenraum vollständig genutzt werden kann, da es keine Verstrebungen oder Verspannungsdrähte gibt.
Die praktische Fertigung erfolgt meistens in mehreren Einzelschalen, die zu einem nahezu runden oder ovalen Querschnitt zusammengenietet oder verklebt werden. Eine Herausforderung stellen Ausschnitte in der Schalenstruktur dar, wobei der zentrale Mittelteil der Schale möglichst von Türen, Luken u. ä. freigehalten werden sollte. Z. B. konnten bei der Vought F-8, die keine Rumpflängsaussteifungen besaß, während der Wartung nicht sämtliche Wartungsklappen gleichzeitig geöffnet werde, da sich ansonsten der Rumpf beim Bewegen verzogen hätte.
Holzbauweise
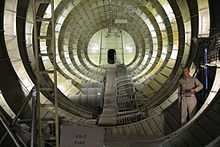
Bei der Holzbauweise werden in der Regel mehrere Lagen Sperrholz, meistens auch in verschiedenen Stärken, übereinander und nebeneinander unter Zuhilfenahme einer Positivform verklebt. Bei der Loughead S-1 wurde dagegen ein Luftsack in einer Negativform eingesetzt, der nach Verschließen der Form aufgeblasen und über 24 Stunden unter Druck gehalten wurde. In den Formen für die Lockheed Vega konnte der Rumpf für drei verschiedene Baumuster hergestellt werden. Je nach Lage und Form der in die Schale geschnittenen Öffnungen, konnte neben der Vega auch die Air Express oder der Tiefdecker Sirius hergestellt werden.
Als Holzsorten kommen z. B. Sitka-Fichte, Birke, Mahagoni und das Holz des Tulpenbaumes zur Anwendung. In Zwischenschichten wird auch Balsaholz eingesetzt. Typische Klebstoffe sind der vor allem historisch interessante Kaseinleim und das aktuelle synthetische Aerodux.
Beispiel Mosquito
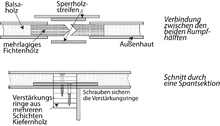
Der Rumpf der De Havilland Mosquito wurde als Monocoque in zwei Halbschalen hergestellt, die mit wenigen Längsaussteifungen auskamen. Zur Herstellung der Schalen war weder Druck noch Wärmezufuhr notwendig. Die zwei etwa 12 m langen Positivformen bestanden entweder aus Mahagoni-Holz, zum Teil wurden aber, z. B. bei der kanadischen Produktion, auch Formen aus Beton eingesetzt. Bei der ersten Baustufe wurden die Rumpfspanten und andere interne Elemente in Schlitze der Form eingebaut. In der zweiten Stufe folgte die Verlegung der inneren Rumpfhaut und der Einbau der strukturellen Bauteile zwischen der inneren und äußeren Sperrholzschicht. Beim hinteren Rumpfteil wurden die Sperrholzstreifen schräg verklebt, um die aus der Torsionsbelastung durch das Leitwerk auftretenden Kräfte besser aufnehmen zu können. Die Maserung der innenliegenden und äußeren Streifen liefen dabei in entgegengesetzten Richtungen.
Aluminium- bzw. Metallbauweise
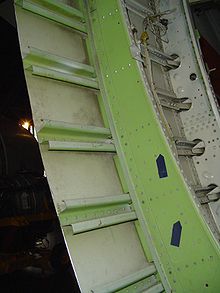
Beplankung
Die Außenhaut ist meist aus gewalztem Alublech besonderer Güte gefertigt. Es wird auf einer Streckmaschine mit Bändern auf eine, der Flugzeugrumpfform entsprechenden Vorrichtung gestreckt und somit in Form gebracht. Durch das Strecken wird gleichzeitig das gewalzte Gefüge verbessert. Meist wird vor dem Aufnieten in einem Säurebad das Außenblech auf die gewünschte Dicke gebracht. An Stellen, an denen das Blech die volle Dicke behalten soll (z.B. im Bereich der Fenster, Türen, Spanten und Stringer) wird ein Schutzlack aufgetragen. An Stellen ohne Schutzlack wird das Alublech chemisch durch die Säure abgetragen. Die Zeit zum Ätzen steuert exakt die Dicke.
Montage der Halbschalen
Die fertigen Halbschalen werden an ihren Spanten und den Außenblechen mit der anderen dazu passenden Halbschale vernietet. Die dabei entstehenden Rumpfabschnitte werden in Längsrichtung an den Stringern und an den Außenblechen vernietet. Durch geringe Überlappung der Stringer, Spanten und Außenblechen beim Vernieten haben diese Verbindungen fast exakt die gleiche Festigkeit wie ein kreisrund gebautes Segment, sind nur minimal schwerer, aber wesentlich billiger in der Herstellung.
Großbaugruppen
Große Verkehrsflugzeuge mit einem oder auch zwei Mittelgängen in der Kabine haben meist einen kreisrunden Querschnitt und werden oft in drei Schalen gefertigt. Das ermöglicht einen günstigen Schiffs-, Luft- oder Straßentransport von Zulieferern zur Endmontagehalle und ein platzsparendes und somit preiswertes Zwischenlagern.
Korrosionsschutz
Flugzeuge unterliegen im Betrieb erheblichen Temperaturschwankungen. Auf einem tropischen Flugplatz sind oft Luftfeuchtigkeiten von bis zu 100 % und Temperaturen von mehr als 40 °C anzutreffen. In Reiseflughöhe (oft +12.000 m) sind die Außentemperaturen im Bereich von ca. −55 °C. Das und die laufende Ausdunstung in der Passagierkabine führen zu einer starken Schwitzwasserbildung und somit zu starker Korrosion. Deshalb müssen alle Aluminiumteile vor der Montage entfettet und lackiert werden. Zwischen die Spanten, Stringer und Bleche muss noch vor der Montage eine gummiartige Zwischenschicht aufgetragen werden. Nach dem Nieten werden alle Verbindungen nochmal mit Korrosionsschutzlack überzogen. Diese Maßnahmen sind im heutigen, internationalen Metallflugzeugbau Standard und garantieren eine übliche Lebens- und Betriebsdauer von ca. 15–40 Jahren.
Beispiel Bf 109
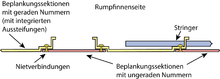
Der Rumpf der Messerschmitt Bf 109 ist ab der Cockpitsektion eine Halbschalenkonstruktion, die vor allem im Hinblick auf eine industrielle Massenfertigung hin optimiert wurde. So wurden die Spanten bereits bei der Herstellung der einzelnen Beplankungselemente durch Aufbiegen der Ränder (Bördeln) in diese integriert. Diese Bearbeitung musste nur an der Hälfte der Segmente (gerade Nummerierung) an beiden Seiten durchgeführt werden. Die andere Hälfte der acht Beplankungsbleche waren lediglich als einfaches Flachblech ausgeführt. Ein Vernieten zusätzlicher Spanten zur Aussteifung war dadurch nicht mehr nötig. Beim Rumpfbau wurden alle Blechsegmente einer Rumpfhälfte auf ein Lehrgerüst aufgespannt und miteinander vernietet. Die Stringer schob man anschließend durch vorbereitete Aussparungen in den „Rahmenaufbiegungen“ und vernietete diese mit der 0,8 mm dicken Duralumin-Außenhaut. Die beiden Rumpfhälften wurden anschließend zusammengefügt, indem innen von oben und unten jeweils ein weiterer extrabreiter Stringer vernietet wurde.
Faserverbundwerkstoffe: GFK und CFK
Prinzip und Werkstoff
Mit Glas- (GFK) oder Kohlenstofffasern (CFK) (engl.: Carbon) verstärkte Kunststoffe sind im Segelflugzeug- und Bootsbau längst bewährte Materialien, die über die Militärluftfahrt (hier: Carbon) nun zunehmend ihre Verbreitung bei Verkehrsflugzeugen findet. Ein Trägermaterial, meist ein Zweikomponenten-Harz, bestehend aus Harz plus eine genau bemessene Menge an Härter, nehmen Teile der Schubkräfte auf. Ein Faserwerkstoff (wie zum Beispiel Glas- oder Kohlenstofffaser) nimmt die Zugspannungen auf. Da Glas- und besonders Kohlenstofffaser sehr hohe Zugspannungen bei geringer Verformung aufnehmen können, haben Teile aus diesen Werkstoff bei niedrigerer Masse eine höhere Steifigkeit und Festigkeit als solche aus Aluminium. Es wird also ein Verbund aus zwei verschiedenen Materialien zu einem neuen mit den Vorteilen von beiden Werkstoffen zusammen. Da der Werkstoff aber spröde ist, sind neue Verfahren und Methoden notwendig, um die für den Flugzeugbau immens wichtige Zähigkeit zu gewährleisten.
Sektionsgröße
Bei Verbundwerkstoffen ist man bestrebt, die Bauteile so groß wie möglich am Stück zu bauen, da jede Verbindungsstelle aufwendig und überlappend verbunden werden muss und somit Kosten- und Schwachpunkt ist. Beim Bau von Segelflugzeugen wird meist der ganze Rumpf vom Cockpit bis zum Seitenleitwerk am Stück laminiert. Bei Großbauteilen, wie z.B. bei der modernen Boeing B787 kann aus wirtschaftlichen Gründen (siehe oben) nicht das ganze Flugzeug „am Stück“ laminiert werden. Bei solchen Dimensionen werden wieder sinnvolle Baugruppen (Sektionen) gebildet.
Positiv/Negativ-Form
Die positive Form des Flugzeugrumpfes wird entweder umgekehrt und direkt als Negativform hergestellt oder von einem sogenannten Urmodell abgeformt. Diese Form wird mit einem Trennwachs behandelt, um ein Festkleben des Werkstoffes an der Form zu verhindern. Die erste Zweikomponenten Harzschicht oder eine spezielle erste Füllschicht wird aufgetragen und bildet später die Außenhaut. In diese Schicht wird eine Lage Glas- oder Kohlenstofffaser gelegt. Darüber kommt wieder eine weitere Lage Fasermaterial. Die folgende Lage wird nun unter einem anderen Winkel (oft kreuzend zur unteren) eingelegt. Bei Prototypen oder Kleinserien von Hand, bei mittelgroßen Serien mit Unterstützung eines Lasermarkierungsgerätes (engl.: „Scanner“) und bei Großserien mit Laminierroboter. So wird Schicht um Schicht zwischen 5 und 20 Lagen aufgebaut. Dies muss relativ zügig geschehen, da ab dem Zusammenmischen von Harz und Härter die „klebeoffene“ Zeit sehr bald abläuft. Die Außenhaut ist nach dem Entformen sehr glatt und muss nur noch minimal bearbeitet werden. Die Innenseite ist oft rau und uneben. Größere Öffnungen für Türen, Fenster oder Klappen sind schon in der Form ausgebildet und durch Legen der Laminatfasern entsprechend dem Umriss entsteht die dort notwendige hohe Steife und tangentiale Zugfestigkeit.
Spanten und Stringer
An besonders hoch belasteten Stellen wie Motor-, Fahrwerk- oder Tragflächenbefestigung werden, ebenso wie im Metall- und Holzflugzeugbau, Schotten, Spanten und auch ggf. Stringer als Versteifung eingebaut. Diese werden in den Ecken in mehreren Lagen mit der Außenhaut verklebt.
Laminier-Richtung und Schichtanzahl
Da (idealerweise) die Spannungsverläufe im Rumpf durch Versuche mit Bruchzellen oder FEM-Methoden vorher bekannt sind, kann die Anzahl der Lagen und die Richtung der Faserstreifen optimal im Voraus bestimmt werden. Je höher die zu erwartende Spannung, desto mehr Lagen. Der Winkel der Lagen zueinander bestimmt dabei maßgeblich die Festigkeit und wird in aufwendigen numerischen Simulationen ermittelt.
Zusammenbau
Die so modellierten Halbschalen haben nach dem Entformen eine Überstand, der entfernt werden muss. Zum Trennen, also dem Entfernen des überschüssigen Randes, werden meist 5-Achs HSC-Fräs- oder Wasserstrahlschneidmaschinen verwendet. In besonderen Montagevorrichtungen werden die Schalenelemente ausgerichtet, fixiert und mit weiteren Lagen Harz plus Faserwerkstoff miteinander überlappend verklebt.
Umweltverträglichkeit, Reparatur, Recycling
Für Aluminium existieren funktionierende Stoffkreisläufe. Für die spröden Faserverbundwerkstoffe müssen diese Instandhaltungsverfahren erst noch entwickelt bzw. in der breiten Anwendung eingerichtet werden. Auch das kostengünstige Reparieren von Beulen, Dellen oder gar Löchern wie sie im Flugplatzalltag durch Kollisionen mit Bodenfahrzeugen schnell vorkommen, muss noch optimiert werden. Der Gewichtsvorteil wiegt diesen Nachteil jedoch über den eingesparten Treibstoff auf. Verlässliche Erfahrungswerte liegen bei den Versicherungsunternehmen noch nicht überall vor.
Beispiel Airbus A350
Beim Airbus A350 wird eine Mischbauweise aus Aluminiumlegierungen und CFK eingesetzt, wobei der CFK-Anteil am gesamten Flugzeug 52 % beträgt. Eine Rumpfsektion des Airbus A350 besteht aus vier CFK-Einzelelementen, die auf Aluminiumspanten aufgenietet werden. Die Stringer bestehen bei der A350 ebenfalls aus CFK und werden bereits in einem vorhergehenden Arbeitsschritt auf die Außenhaut aufgeklebt.



© biancahoegel.de
Datum der letzten Änderung: Jena, den: 06.06. 2023