Faserverbundwerkstoff
Ein Faserverbundwerkstoff ist ein aus im Allgemeinen zwei Hauptkomponenten (eine bettende Matrix und verstärkende Fasern) bestehender Mehrphasen- oder Mischwerkstoff. Durch gegenseitige Wechselwirkungen der beiden Komponenten erhält dieser höherwertige Eigenschaften als jeder der beiden einzeln beteiligten Komponenten.
Allgemeines
Mechanische Eigenschaften verschiedener FVK-Laminate (Faservolumenanteil 40%), Quelle: OUV | ||||
Glasfaser | Aramidfaser | Kohlefaser | ||
---|---|---|---|---|
spezifisches Gewicht | g / cm3 | 1,7 | 1,25 | 1,4 |
Zugfestigkeit | N / mm2 | 420 - 800 | 450 - 800 | 550 - 850 |
E-Modul (Zug) | kN / mm2 | 15 - 29 | 24 - 42 | 44 - 85 |
Bruchdehnung | % | 2,5 - 3,5 | 2,5 | 1,0 - 1,3 |
Druckfestigkeit | N / mm2 | 440 - 650 | 120 - 150 | 500 - 750 |
E-Modul (Druck) | kN / mm2 | 14 - 28 | 12 - 21 | 42 - 80 |
Biegefestigkeit | N / mm2 | 450 - 800 | 270 - 330 | 550 - 870 |
E-Modul (Biegung) | kN / mm2 | 15 - 30 | 26 - 50 | 47 - 80 |
Im Unterschied zu bisherigen Verbundwerkstoffen, wie zum Beispiel Stahlbeton, wird mit der Einführung extrem dünner Fasern (einige μm Durchmesser) unter Anderem der Effekt der spezifischen Festigkeit genutzt. Dieser Zusammenhang wurde in den zwanziger Jahren von Griffith entdeckt und lautet: Ein Werkstoff in Faserform hat in Faserrichtung eine vielfach größere Festigkeit als dasselbe Material in anderer Form. Je dünner die Faser ist, desto größer ist ihre Festigkeit. Die Ursache hierfür liegt in einer zunehmenden Gleichrichtung der Molekülketten mit abnehmender zur Verfügung stehender Fläche. Zudem werden zum Bruch führende Fehlstellen (weakest link theory) im Material auf sehr große Abstände verteilt, sodass die Fasern weitgehend frei von Fehlstellen sind, die einen Bruch verursachen können. Da bei gleicher Festigkeit die schwere, feste Komponente eingespart und durch eine leichtere ersetzt werden kann, entsteht ein Werkstoff mit einer hohen spezifischen Festigkeit (Verhältnis aus Festigkeit und Gewicht). Außerdem führt ein Fehler im Material nicht zum Versagen des gesamten Bauteils, sondern vorerst nur zum Bruch einer einzelnen Faser im Verbund.
Da die Fasern je nach Beanspruchung ausgerichtet und in ihrer Dichte (Anzahl pro Fläche) angepasst werden können, entstehen mit Hilfe entsprechender Herstellungsverfahren maßgeschneiderte Bauteile. Um die Festigkeit in verschiedene Richtungen zu beeinflussen, werden statt einzelner Fasern Gewebe oder Gelege verwendet, die vor dem Kontakt mit der Matrix hergestellt werden.
Funktionsweise
Die höherwertigen Eigenschaften eines Faserverbundwerkstoffes werden erst durch das Zusammenspiel beider Komponenten erreicht. Aus zwei Komponenten ergeben sich somit drei wirkende Phasen im Material: Sehr zugfeste Fasern, eine relativ weiche, sie bettende Matrix und eine beide Komponenten verbindende Grenzschicht.
Bedingungen für die Verstärkungswirkung von Fasern
Nicht alle Kombinationen von Faser- und Matrixwerkstoffen führen zu einer Erhöhung der Festigkeit und der Steifigkeit des neuen Verbundes. Es müssen drei Bedingungen erfüllt sein, damit in faserparalleler Richtung eine Verstärkungswirkung eintritt:
- EFaser, längs > EMatrix
Der Elastizitätsmodul der Faser in Längsrichtung muss größer sein als der Elastizitätsmodul des Matrixwerkstoffs. - εBruch, Matrix > εBruch, Faser
Die Bruchdehnung des Matrixwerkstoffs muss größer sein als die Bruchdehnung der Fasern. - RFaser, längs > RMatrix
Die Bruchfestigkeit der Fasern muss größer sein als die Bruchfestigkeit des Matrixwerkstoffs.
Senkrecht zur Faser tritt in der Regel keine Steigerung der Festigkeiten auf.
Aufgaben der Komponenten
- Die Matrix gibt dem Faserverbundwerkstoff sein Aussehen. Sowohl der Farbe als auch der Oberflächenstruktur sind wenig Grenzen gesetzt. In mechanischer Hinsicht muss sie die verstärkenden Fasern in ihrer Position halten und Spannungen zwischen ihnen übertragen und verteilen. In Bezug auf die Dauerhaftigkeit hat sie die Aufgabe, die Fasern vor äußeren mechanischen und chemischen Einflüssen zu schützen.
- Die Fasern geben dem Faserverbundwerkstoff die notwendige Festigkeit. Neben der Zugfestigkeit kann, falls der Werkstoff auf Druck beansprucht wird, auch die Biegefestigkeit eine Rolle spielen.
- Die Grenzschicht dient der Spannungsübertragung zwischen den beiden Komponenten. Sie überträgt ausschließlich Schub und kann sehr abstrakte Formen annehmen wenn der Schub beispielsweise über reine Reibung erfolgt. In anderen Fällen jedoch, beispielsweise bei Schub über Klebehaftung, ist sie herstellungstechnisch gewollt und physisch vorhanden. Im letzteren Fall werden die Fasern vor dem ersten Kontakt mit der Matrix mit einem Kopplungsmittel beschichtet, welches chemisch mit beiden Komponenten reagieren kann und einen möglichst ununterbrochenen Übergang garantiert.
Ein wichtiger Faktor bei der Bemessung von Faserverbundwerkstoffen ist das Volumenverhältnis (Faservolumenanteil) zwischen Fasern und Matrix. Je höher der Anteil an Fasern ist, desto fester, jedoch auch starrer und spröder wird der Werkstoff. Dies kann zu Problemen führen, wenn gewisse Verformungen überschritten werden.
Prinzip der Kraftübertragung
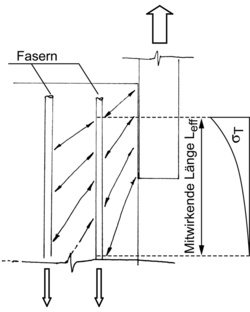
Wie in Abbildung 1 dargestellt, ist es im Falle einer konzentriert aufgebrachten Zugkraft unmöglich, diese direkt an den Fasern angreifen zu lassen, da diese immer von einer Matrixschicht überdeckt sind. Die Zugkraft wirkt somit nur auf die Matrix in Form von konzentrierten Spannungen und wird von dieser auf die nächstliegendsten Fasern verteilt. Die Größe dieses "Ausbreitfeldes" (die mitwirkende Länge einer Faser) hängt vom Spannungsverhältnis zwischen Faser und Matrix ab: Eine weiche Matrix kombiniert mit steifen Fasern ergeben große mitwirkende Längen, eine steife Matrix mit weichen Fasern ergibt kleine mitwirkende Längen. Spannungen müssen jedoch nicht unbedingt in konzentrierter Form aufgebracht werden, eine Variante zur Erzeugung von Zugspannungen ist zum Beispiel ein aufgebrachtes Moment. Das Wirkungsprinzip ändert sich nicht.
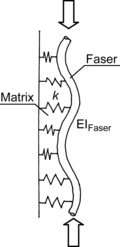
Im Falle von längs zum Faserverlauf wirkendem Druck, wie er auch bei Biegung auftritt, funktioniert die Matrix wie eine Bettung und die Faser (das Faserbündel) wie ein elastisch gebetteter Balken, siehe auch Abbildung 2. Hier sind wichtige Materialeigenschaften die Matrixsteifigkeit k und die Biegesteifigkeit der Faser E · I (Steifigkeit multipliziert mit dem Flächenträgheitsmoment). Die Berechnung wird nun sehr viel komplexer, da nun außer der schieren Zugfestigkeit der Faser auch deren Durchmesser wegen des Flächenträgheitsmoments eine Rolle spielt. Der Fall Druck wird seit Mitte der sechziger Jahre des 20. Jahrhunderts erforscht und stellt noch heute eine wissenschaftliche Herausforderung dar. Durch Rechnereinsatz und moderner FEM Programme wird gegenwärtig versucht, die theoretischen Ansätze numerisch zu beweisen und nachzuvollziehen. Die Probleme liegen einerseits in der Tatsache, dass es sich um ein Stabilitätsproblem handelt und somit schon kleinste Veränderungen in der Werkstoffzusammensetzung erhebliche Auswirkungen auf die ertragbaren Kräfte haben können. Zum anderen versagt ein hochentwickelter Mehrphasenwerkstoff in vielfältiger Weise und unterschiedliche Mechanismen wechseln sich während des Versagens ab und bedingen sich teilweise gegenseitig. Druckversagen findet sehr plötzlich, schnell und teilweise ohne Vorwarnung statt. Somit ist er sehr schlecht zu beobachten, was die Analyse erschwert.
Materialien
Neben den rein mechanischen Eigenschaften, also der notwendigen berechneten Festigkeit, spielen vor allem Dauerhaftigkeits- und Preisfragen eine große Rolle bei der Wahl der Materialien. Um ein gutes Funktionieren zu gewährleisten, sollten die Steifigkeiten der beiden Komponenten aufeinander abgestimmt werden, so dass sich auftretende Kraftspitzen gut im Material verteilen können. Im einzelnen werden folgende Materialien eingesetzt
Fasern
- Glasfasern
Glasfasern sind hauptsächlich wegen ihres relativ geringen Preises die am häufigsten verwendeten Fasertypen. Es gibt Glasfasertypen für unterschiedliche Einsatzgebiete. - Kohlenstofffasern
- Keramikfasern
Endlose Keramikfasern aus Aluminiumoxid, Mullit (Mischoxid aus Aluminiumoxid und Siliciumdioxid), SiBCN, SiCN, SiC etc. sind teure Spezialfasern für hochtemperaturbelastbare Verbundwerkstoffe mit einer Keramikmatrix. Die nicht-oxidischen Fasern werden, ähnlich wie Kohlenstofffasern, aus organischen Harzen gewonnen, in denen neben Kohlenstoff auch Silicium enthalten ist. - Aramidfasern
- Borfasern
- Stahlfasern
- Naturfasern
- Nylonfasern
Fasern mit einer hohen Bruchdehnung sind von Vorteil, wenn das Bauteil Stöße aufnehmen muss und diese Eigenschaft für die Bemessung maßgebend ist.
Matrix
Die Wahl der Matrix teilt die Faserverbundwerkstoffe in zwei Gruppen: Faser-Kunststoff-Verbunde (verstärkter Kunststoff, faserverstärkte Kunststoffe) und Andere.
- Faser-Kunststoff-Verbund
Als Matrix werden die folgenden Harze eingesetzt:- Duromere (weitere Bezeichnungen: Duroplast, Kunstharze)
- Elastomere
- Thermoplaste
Während die Kunstharze und Elastomere bis zu ihrer Aushärtung flüssig vorliegen, sind Thermoplaste bis ca. 150 °C (teilweise bis 340 °C) fest. Die duroplastischen Kunstharze sind in der Regel glassspröde und verformen sich nicht plastisch. Faserverstärkte Kunststoffe aus Thermoplaste lassen sich unter Hitze nachträglich umformen.
Die Mikro- und Makrotränkung der Fasern ist bei Kunstharzen einfacher als bei festen Thermoplasten. Thermoplaste werden zur Tränkung erhitzt oder in einem Lösungsmittel gelöst.
- Andere
- Zement und Beton
- Metalle
- Keramiken als Matrix für nichtspröde Keramische Faserverbundwerkstoffe
- Kohlenstoff Kohlenstofffaserverstärkter Kohlenstoff (CFC)
Typen und Herstellungsverfahren
Laminate
Diese Gruppe nutzt alle Vorteile der individuellen Faserausrichtung. Sie bestehen meist aus mehreren übereinander gelegten Fasermatten mit unterschiedlichen Hauptfaserrichtungen. Für ihre Herstellung gibt es mehrere Verfahren:
- Handlegeverfahren
Die Faserhalbzeuge (Gewebe/Gelege/Fasermatten) werden von Hand in eine Form eingelegt und mit Kunstharz getränkt. Anschließend werden sie mit Hilfe einer Rolle durch Anpressen entlüftet. Dadurch soll nicht nur die im Laminataufbau vorhandene Luft, sondern auch überschüssiges Harz entfernt werden. Dieses Vorgehen wird so oft wiederholt, bis die gewünschte Schichtstärke vorhanden ist. Man spricht auch von einem "Nass in Nass"-Verfahren. Nach dem Aufbringen aller Schichten härtet das Bauteil durch die chemische Reaktion des Harzes mit dem Härter aus. Das Verfahren stellt keine großen Ansprüche an die Werkzeuge und ist auch für sehr große Bauteile geeignet. Es wird oft im Serienbau eingesetzt, wo zwar leichte Bauteile erwünscht sind, aber auch kostengünstig produziert werden soll.
Vorteile sind geringer Werkzeug- und Ausstattungsaufwand, dem gegenüber stehen die geringere Bauteilqualität (geringerer Fasergehalt) und der hohe manuelle Aufwand, der geschulte Laminierer voraussetzt. Die offene Verarbeitung des Harzes stellt hohe Ansprüche an den Arbeitsschutz. - Handauflegen mit Vakuumpressen
Nach dem Einbringen aller Verstärkungs- und Sandwichmaterialen wird die Form mit einer Trennfolie, einem Absaugvlies und einer Vakuumfolie abgedeckt. Zwischen der Vakuumfolie und der Form wird ein Unterdruck erzeugt. Dieser bewirkt, dass der Verbund zusammengepresst wird. Eventuell noch enthaltene Luft wird abgesaugt. Überschüssiges Harz wird vom Absaugvlies aufgenommen. So kann gegenüber dem Handauflegeverfahren eine noch höhere Bauteilqualität erzielt werden. - Prepreg-Technologie
Mit Matrixwerkstoff vorimprägnierte (also bereits getränkte) Fasermatten werden auf die Form aufgelegt. Das Harz ist dabei nicht mehr flüssig, sondern hat eine leicht klebrige feste Konsistenz. Der Verbund wird anschließend mittels Vakuumsack entlüftet und danach, häufig im Autoklaven, unter Druck und Hitze ausgehärtet. Das Prepregverfahren ist aufgrund der notwendigen Betriebsausstattung (Kühlanlagen, Autoklav) und der anspruchsvollen Prozessführung (Temperaturmanagement) eines der teuersten Herstellungsverfahren. Es ermöglicht neben dem Faserwickeln und den Injektions- und Infusionsverfahren jedoch die höchsten Bauteilqualitäten. Das Verfahren findet vor allem in der Luft- und Raumfahrt, im Motorsport, sowie für Leistungssportgeräte Anwendung.
- Vakuum-Infusion
VakuumaufbauFertiges Bauteil - Faserwickeln
Das Faserwickelverfahren ist eine Technik zum Ablegen von Endlosfasersträngen (Rovings) auf einer (zumindest annähernd) zylindrischen Form. Mit diesem Verfahren werden Fasern sehr straff und eng aneinander liegend mit einer hohen Maßgenauigkeit positioniert. Zum Wickeln der Fasern ist ein Körper notwendig, der dem Bauteil seine spätere Gestalt gibt. Diesen Körper nennt man wie beim Urformen üblich Kern. Auch beim Faserwickeln unterscheidet man zwischen verlorenen und wiederverwendbaren Kernen.
Verlorene Kerne werden meist aus leichtem Hartschaum gefertigt, der entweder im Bauteil verbleibt oder chemisch aufgelöst wird.
Bei gewickelten Druckbehältern besteht die Besonderheit darin, dass der dünnwandige Kern (zum Beispiel aus HD-Polylethylen bestehend) als gasdichte Barriere im Inneren verbleibt. Sind diese sogenannten Liner aus Metall, dann können sie auch mittragend sein und bilden zusammen mit der Matrix aus Verbundwerkstoff ein Hybrid-System. Hier ist der Kern zwar auch "verloren", ist aber gleichzeitig funktionaler Bestandteil der Konstruktion.
Wiederverwendbare Kerne sind meist aus Aluminium gefertigt; sie schränken naturgemäß die Gestaltungsfreiheit bei der Konstruktion ein, da sich der Kern aus dem Bauteil entfernen lassen muß.
Beispiele für fasergewickelte Teile sind Leuchttürme, Hüllen von Straßenbahnwaggons und Bussen oder Silos.
Als Tränkverfahren sind üblich:- Die Endlosfaser beziehungsweise der Strang wird zunächst durch ein Tränkbad geführt, in dem sie mit dem Matrixwerkstoff benetzt wird und dann um eine Form gewickelt wird.
- Es werden Prepreg-Faserbahnen aufgewickelt, die erst durch Erwärmen ausgehärtet werden.
- Es werden ungetränkte Fasern gewickelt, die danach mit einem Harzinjektionsverfahren (siehe oben) getränkt werden.
- Faserspritzen
Das Faserspritzen ist strenggenommen keine Laminiertechnik, da das Material nicht im Schichten (lat.: lamina) aufgebracht wird. Das Ergebnis und die Anwendung des Materials sind jedoch vergleichbar mit laminierten Produkten, daher wird diese Technik hier mit aufgeführt.
Beim Faserspritzen werden Endlosfasern (Rovings) von einem Schneidwerk auf die gewünschte Länge geschnitten und zusammen mit Harz und Härter mittels einer Faserspritzpistole in die Form gebracht. Zusätzlich verwendet man wie beim Handlaminieren eine Laminierrolle, um das Laminat zu verdichten. Der grösste Nachteil dieser Variante ist die deutlich geringere Festigkeit gegenüber laminiertem Gewebe.
Spritzgussteile
Isotrope faserverstärkte Kunststoffe werden kostengünstig im Spritzgussverfahren hergestellt. Die Kurzfasern (max. wenige Millimeter lang) werden dabei zusammen mit dem Matrixwerkstoff in die Form gespritzt.
Spritzpressteile
Beim Spritzpressen oder auch Resin Transfer Moulding (RTM) können trockenen Fasern in eine Form eingelegt werden und anschließend mit flüssigem Harz unter Druck umströmt werden. Durch Wärme wird das Harz ausgehärtet. Die Faserorientierung kann dabei durch Näh- und Stickverfahren im Vorformling durch gezieltes Ablegen den Lastfällen angepasst werden.
Strangziehteile
Profile mit kleineren Dimensionen und gleich bleibenden Querschnitten werden sehr effizient im Strangziehverfahren hergestellt. Dabei sind alle Fasern unidirektional in Längsrichtung des Rohres ausgerichtet, was zu sehr guter Zug-, Druck- und Biegefestigkeit führt.
Sheet Molding Compounds (SMC)
Bei dieser Art von faserverstärkten Kunststoffen wird in einer Vorfertigung aus Harzen, Härtern, Füllstoffen, Additiven, etc. und Glasfaserstücken bis 50 mm Länge eine sogenannte Harzmatte gefertigt. Nach eine Reifezeit (Lagerzeit), einige Tage bei ca. 30-40 °C, erhöht sich die Viskosität der Harzmatte von honigartig auf wachsfest bis lederartig. Bei dieser definiert festzulegenden Viskosität, abhängig von der Harzmattenrezeptur kann die Matte weiterverarbeitet werden.
Die Weiterverarbeitung erfolgt dann in beheizten Werkzeugen im Pressverfahren. Die Harzmatte wird, je nach Bauteilgröße und -geometrie, in genau definierte Größen zerschnitten und nach einem definierten Einlegeplan im Werkzeug platziert. Beim Schließen der Presse wird die Harzmatte im gesamten Werkzeug verteilt. Hierbei sinkt die vorher während der Reifezeit erreichte Viskositätserhöhung fast wieder auf des Niveau der Halbzeugfertigung.
Dabei kommt es zu zwei Phänomenen:
- Das Fließen der Harzmatte im Werkzeug hat zur Folge, dass es an den Ecken des Werkzeuges (aber auch an Verstärkungsrippen und Domen) zu einem Aufeinandertreffen von verschiedenen Fließfronten kommen kann. Bei nicht ausreichender Durchdringung der Fließfronten kommt es dann zu sogenannten Bindenähten. An diesen Bindennähten sind die mechanischen Eigenschaften des Bauteils teilweise deutlich reduziert gegenüber dem übrigen Bauteil.
- Die leichteren und feineren Bestandteile der Harzmatte (Harze, Additive etc.) fließen schneller als die größeren Bestandteile (Glasfasern, Füllstoffe). Dadurch kann es bei langen Fließwegen an den Bauteilgrenzen zu einer Anreicherung der kleineren Bestandteile kommen, es bildet sich eine "Harzschicht" aus. Diese Harzschicht ist spröde und kann zu kleineren Abplatzungen bei mechanischer Beanspruchung führen.
Der Vorteil dieser Werkstoffklasse liegt in der leichten Darstellung dreidimensionaler Geometrien und Wanddickenunterschieden in nur einem Arbeitsschritt. Die endgültige Bauteilform wird durch die Kavität eines mindestens zweiteiligen Werkzeugs gegeben und zeigt üblicherweise beidseitig glatte, optisch ansprechende Oberflächen.
Nach einer Aushärtezeit von 30 Sekunden bis mehreren Minuten bei Temperaturen von 140 °C bis 160 °C - deren Dauer und Höhe von der Bauteildicke und dem verwendeten Reaktionssystem abhängt - kann das fertige Bauteil aus der Form entnommen werden, muss aber aufgrund der noch hohen Bauteiltemperaturen vorsichtig gleichmäßig gekühlt werden, damit es nicht zu Mikrorissen im Bauteil kommt. SMC-Bauteile sind - aufgrund der größeren Faserlänge als bei BMC - in der Regel höher belastbar als BMC-Bauteile. SMC-Bauteile können bei entsprechender Auslegung auch in lackierten Sichtbereichen eingesetzt werden.
Faserbeton
Die Zugfestigkeit von Beton oder Zement kann durch Beigabe von Fasern erhöht werden. Die Fasern haben nur wenige Zentimeter Länge (der hohe E-Modul des Betons macht lange Fasern unsinnig) und werden orientierungslos in der Matrix verteilt. Das Ergebnis ist ein isotroper Werkstoff. Die Fasern werden wie normaler Zuschlag mit dem Beton angerührt und zusammen in einer Schalung ausgehärtet.
Sicherheitsvorkehrungen bei der Verarbeitung
Schutzbrille und Schutzhandschuhe stellen einen Mindestschutz vor dem Kontakt mit dem Harzsystem her. Harz und speziell Härter und Beschleuniger enthaltenen häufig Stoffe, die neben ihrer Giftigkeit auch allergiefördernd wirken. Im ausgehärteten Zustand wird hingegen teilweise sogar Lebensmittelechtheit erreicht.
Beschleuniger und Härter werden nie direkt zusammengegeben. Beide Komponenten können heftig miteinander reagieren, dabei besteht Verletzungsgefahr. Deshalb wird der Beschleuniger in aller Regel vor dem Vermischen mit dem Härter dem Harz zugegeben.
Beim mechanischen Bearbeiten (Zerspanen) von faserverstärkten Kunststoffen entstehen sehr feine Partikel die je nach Fasertyp lungengängig sein können. Deshalb ist ein Mundschutz obligatorisch.
Kohlenstofffaserstaub kann durch seine elektrische Leitfähigkeit elektrische Geräte beschädigen. Daher wird die Bearbeitung unter Explosions-Schutz durchgeführt.
Anwendungsgebiete
Faserverbundwerkstoffe umgeben uns in allen Lebensbereichen, meist ohne dass wir uns dessen bewusst sind. Das Spektrum reicht von Kleidern, Möbeln, Haushaltsgeräten bis hin zu mehrstöckigen Bauwerken, Brücken, Booten und der Luft- und Raumfahrt.
Berechnung der elastischen Eigenschaften
Die elastischen Eigenschaften von Faserverbundwerkstoffen werden auf der Grundlage der Eigenschaften von elementaren Einzelschichten berechnet (unidirektionale Schichten). Dieses Berechnungsverfahren ist als klassische Laminattheorie bekannt. Gewebe werden dabei als zwei, in einem Winkel von 90° gedrehte, unidirektionale Schichten abgebildet. Einflüsse durch die Ondulation der Fasern im Gewebe werden durch Abminderungsfaktoren berücksichtigt. Eine Entwurfsmethode für gewichtsoptimale Laminate ist die Netztheorie.
Ergebnis der klassischen Laminattheorie sind die sogenannten
Ingenieurskonstanten des Verbundwerkstoffs
und die Scheiben-Platten-Steifigkeitsmatrix. Diese Matrix besteht aus folgenden
Elementen:
- Scheibensteifigkeits-Matrix A
- Plattensteifigkeits-Matrix D
- Koppel-Matrix B
Anhand dieser Matrizen können die Reaktionen des Verbundwerkstoffs auf
- Scheibenbelastungen: Normalspannungen σ1,σ2 und Schub τ12 in der Ebene
- Plattenbelastungen: Biegemomente m1,m2 und Drillmoment m12
berechnet werden.
Die Koppel-Matrix koppelt dabei die Scheibenbelastungen mit den Plattenverformungen und umgekehrt. Für die Praxis von Interesse ist, dass eine besetzte Koppel-Matrix zu thermischen Verzug führt. Da auch thermische Dehnungen gekoppelt werden, verziehen sich Faserverbundbauteile, deren Koppelmatrix besetzt ist. Ziel vieler Forschungsvorhaben ist es, die Kopplungen in der Scheiben-Platten-Steifigkeitsmatrix gezielt konstruktiv zu nutzen.
Für den genauen Berechnungsablauf sei auf die Literatur und Lehrbücher verwiesen.
Berechnung und Nachweis
Der Festigkeitsnachweis, insbesondere von Faserkunststoffverbunden, erfolgt über Bruchkriterien. Aufgrund der Festigkeitsanisotropie der meisten Faserverbundwerkstoffe sind spezielle Bruchkriterien für Faserkunststoffverbunde notwendig.
Es existiert eine Vielzahl unterschiedlicher Bruchkriterien und damit auch Nachweismethoden. Oft haben einzelne Firmen (zum Beispiel im militärischen oder zivilen Großflugzeugbau) eigene Nachweisverfahren entwickelt.
Natürlicher Faserverbundwerkstoff
Holz in seiner natürlich gewachsenen Form ist häufig Vorlage bei der Auslegung von Faser-Kunststoff-Verbunden. Die Ursache hierfür ist, dass Holzfasern, genau wie andere Naturfasern, aus unterschiedlichen "Einzelbausteinen" zusammengesetzt sind. Steife Cellulosefibrillen sind in eine Matrix aus Hemicellulose und Lignin eingebettet und dienen als festigendes Element in der Zellwand. Auch in seinen künstlich geschaffenen Formen Pressspan oder MDF werden zumindest die Naturfasern als Komponente eingebracht.
Knochen ist ein Faserverbundwerkstoff in zweierlei Hinsicht: im Nanometerbereich sind die Kollagenfasern eingebettet in Hydroxylaprn, genau wie andere Naturfasern, aus unterschiedlichen "Einzelbausteinen" zusammengesetzt sind. Steife Cellulosefibrillen sind in eine Matrix aus Hemicellulose und Lignin eingebettet und dienen als festigendes Element in der Zellwand. Auch in seinen künstlich geschaffenen Formen Pressspan oder MDF werden zumindest die Naturfasern als Komponente eingebracht.
Knochen ist ein Faserverbundwerkstoff in zweierlei Hinsicht: im Nanometerbereich sind die Kollagenfasern eingebettet in Hydroxylapatitkristalle, in kortikalem Knochen im Mikrometerbereich wirken Osteons zusätzlich als Fasern.

© biancahoegel.de
Datum der letzten Änderung: Jena, den: 06.03. 2021