Produktionsprozess
veg.: Glas
Man nehme..
Die Tontafelbibliothek des assyrischen Königs Assubanipal (7. Jh. v. Chr.) enthält das älteste überlieferte Glasrezept:
"Nimm 60 Teile Sand, 180 Teile Asche aus Meerespflanzen, 5 Teile Kreide - und Du erhältst Glas."
Gemenge
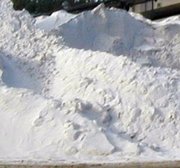
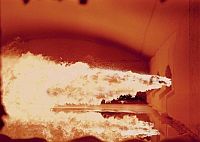
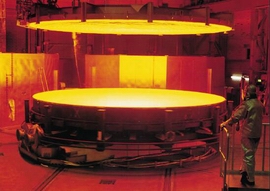
Es gibt heute kaum ein Element, das nicht in irgendeiner Form bei der Glasherstellung Verwendung finden kann.
Für die Herstellung von Kalk-Natron-Glas, das ca. 90% der produzierten Glasmenge ausmacht, werden unter anderem folgende Rohstoffe eingesetzt:
- Quarzsand als fast reiner SiO2-Träger zur Netzwerkbildung. Wichtig ist, dass der Sand nur einen geringen Anteil an Fe2O3 besitzen darf (< 0,05%), da sonst bei Weißglas störende Grünfärbungen auftreten.
- Natriumcarbonat (Mineral: Natrit; Na2CO3) dient als Natriumoxidträger, das als Netzwerkwandler und als Flussmittel dient und den Schmelzpunkt des SiO2 senkt. In der Schmelze wird Kohlensäure frei und muss aus dem Glas entfernt werden. Natrium wird als Nitrat oder Sulfat (Natriumsulfat ist Läutermittel zur Reduzierung des Blasengehaltes) der Schmelze zugeführt.
- Pottasche (K2CO3) liefert Kaliumoxid für die Schmelze, das wie Natriumoxid als Netzwerkwandler und Flussmittel dient.
- Feldspat (NaAlSi3O8) trägt neben SiO2 und Na2O Tonerde (Al2O3) in das Gemenge ein. Diese führt zu einer Erhöhung der chemischen Beständigkeit gegenüber Wasser, Nahrungsmitteln und Umwelteinflüssen.
- Kalk dient als Netzwerkwandler. Bei der Schmelze wandelt es sich zu Kohlendioxid und Calciumoxid. CaO erhöht in mäßiger Zugabe (10 - 15%) die Härte und chemische Beständigkeit.
- Dolomit ist ein Träger für CaO und MgO. Magnesiumoxid hat ähnliche Eigenschaften wie Calciumoxid auf die Schmelze. Ein zu hoher MgO-Gehalt im Glas kann jedoch die Liquidustemperatur unerwünscht erhöhen.
- Altglas oder Eigenscherben aus dem Produktionsbruch werden ebenfalls dem Gemenge wiederaufgegeben - Altglas aus dem Glasrecycling allerdings nur in der Behälterglasindustrie, wo ihr Anteil bis über 90% betragen kann. Neben eingespartem Rohstoff macht sich dieses im geringeren Energieverbrauch bemerkbar, da Scherben leichter schmelzen als das Gemenge. Probleme beim Altglasrecycling sind eine schlechte Farbtrennung, Fremdbestandteile wie Metalle, Keramik oder Spezialgläser. Die Fremdstoffe verursachen Glasfehler durch nicht vollständiges Aufschmelzen und Schäden in der Glasschmelzwanne, da sich Metalle in den feuerfesten Boden einfressen.
Für Spezialgläser kommen auch Mennige, Borax, Bariumcarbonat und „Seltene Erden“ zum Einsatz.
Eine Sonderform stellt das Kieselglas dar, das man durch Schmelzen von reinem Quarz (Bergkristall) bei > 1.800 °C erhält.
Schmelze
Das Schmelzen des Glases erfolgt in Wannen- oder Hafenöfen.
Bei ersteren dient der Ofenraum selbst als Schmelzgefäß (Wanne — mittleres Bild). Die Hafenöfen enthalten runde topfartige Gefäße, die Häfen,
die eine Größe bis zu 1.000 Liter haben und aus Spezialtonen und Kaolin im Gemisch mit Schamotte hergestellt sind. Die Häfen werden nach monatelanger Trocknung langsam immer höher erhitzt und
schließlich bei etwa 1.500 °C im Schmelzofen dichtgebrannt.
Glasschmelzöfen für optische Gläser haben im allgemeinen nur einen einzigen Hafen, Öfen für technische Gläser enthalten mehrere Häfen. Technische Massengläßer werden
fast außschließlich im kontinuierlichem Betrieb in Wannen geschmolzen.
Die Glasschmelzöfen sind heute gas- oder ölbeheitzt. In bestimmten Fällen werden elektrisch beheitze Schmelzöfen benutzt. Insbesondere zum Erschmelzen optische Spezialgläßer werden induktiv erwärmte Platinwannen oder Quarzwannen benutzt. Bei tieferen Schmelztemperaturen können auch mit Hochfrequenz kapaziviv erwärmte Wannen benutzt werden.
Die Glasschmelze besteht aus verschiedenen Phasen: Den Beginn macht die Rauhschmelze mit dem Erschmelzen des Gemenges. Dieses umfasst die Rauhschmelze und die Homogenisierung. Nach dem Erschmelzen der festen Bestandteile kommt die Läuterung, in der die Gase in der Schmelze ausgetrieben werden. Daran schließt sich das Abstehen des Glases an, in der das Material zur weiteren Formgebung abgekühlt wird.
Bei chargenweise arbeitenden Tageswannen und Hafenöfen geschehen alle diese Schritte nacheinander in demselben Becken. Dieses historische Produktionsverfahren findet heute nur noch bei kunsthandwerklicher Produktion und speziellen, optischen Gläsern statt. Im industriellen Maßstab finden ausschließlich kontinuierlich arbeitende Öfen Verwendung. Hier ist die Abfolge obiger Schritte nicht zeitlich, sondern räumlich getrennt. Die Menge der Glasentnahme entspricht der des zugeführten Gemenges.
Das Gemenge wird mit einer Einlegemaschine der Schmelzwanne aufgegeben. Bei Temperaturen von ca. 1480 °C schmelzen die verschiedenen Bestandteile langsam. Die Bewegung der Konvektion im Glasbad erzeugt Homogenität. Diese kann durch ein Bubbling, der Eindüsung von Luft oder Gasen in die Schmelze, unterstützt werden.
Im Läuterbereich, der dem Schmelzbereich unmittelbar folgt und häufiger auch durch einen Wall in der Schmelze von diesem getrennt ist, werden in der Schmelze verbliebene Blasen ausgetrieben. Durch die hohe Zähigkeit der Schmelze geschieht dieses nur sehr allmählich, und es sind ebenso hohe Temperaturen erforderlich wie im Schmelzbereich. Da die Läuterung bestimmend für die Glasqualität ist, gibt es vielfältige Maßnahmen, um diese zu unterstützen.
Dem Läuterbereich schließt sich die baulich klar getrennte Arbeitswanne an. Da für die Formgebung niedrigere Temperaturen als zur Schmelze und Läuterung nötig sind, muss das Glas vorher abstehen. Daher spricht man auch von Abstehwanne. Der Kanal, der Schmelzwanne und Arbeitswanne verbindet, heißt Durchfluss und arbeitet nach dem Siphonprinzip. Bei Flachglaswannen sind Schmelz- und Arbeitswanne nur durch eine Einschnürung getrennt, da ein Durchfluss eine optische Unruhe im Fertigprodukt entstehen ließe.
Von der Arbeitswanne fließt das Glas weiter zum Punkt der Entnahme. Bei der Produktion von Hohlglas sind dieses die Speiser oder Feeder. Hier werden Tropfen in darunter stehende Glasmaschinen geleitet. Bei Flachglas fließt das Glas über die Lippe in das Floatbad.
Einstellung der Glaseigenschaften
Glaseigenschaften können mittels statistischer Analyse von Glas-Datenbanken wie z.B. von SciGlass® oder Interglad® ermittelt und optimiert werden. Insofern die gewünschte Glaseigenschaft nicht mit Kristallisation (z.B. Liquidustemperatur) oder Phasentrennung in Zusammenhang steht, ist einfache lineare Regressionsanalyse anwendbar, unter Zuhilfenahme polynomer Gleichungen der ersten bis zur dritten Ordnung. Untenstehend ist eine Gleichung zweiter Ordnung als Beispiel, wobei C die Konzentrationen der Glaskomponenten wie Na2O oder CaO darstellen. Die b-Werte sind variable Koeffizienten, und n ist die Anzahl aller Glaskomponenten. Der Glas-Hauptbestandteil SiO2 ist in der dargestellten Gleichung ausgeschlossen und wird mit der Konstante bo berücksichtigt. Der Großteil der Glieder in der Beispielgleichung kann aufgrund von Korrelations- und Signifikanzanalyse vernachlässigt werden.
Die Liquidustemperatur wurde von C. Dreyfus und G. Dreyfus mittels
Neural-Networks-Regression modelliert.
In der Industrie ist es oft erforderlich, mehrere Glaseigenschaften, einschließlich der Produktionskosten, gleichzeitig zu optimieren. Dies geschieht mit der Methode der kleinsten Quadrate, wodurch der Abstand zwischen den gewünschten Eigenschaften und den vorausberechneten einer fiktiven Glassorte durch Variation dessen Zusammensetzung minimiert wird. Es ist möglich, die gewünschten Eigenschaften unterschiedlich zu wichten.
Glasart | SiO2 | Al2O3 | Na2O | K2O | MgO | CaO | B2O3 | PbO | TiO2 | F | As | Se | Ge | Te |
---|---|---|---|---|---|---|---|---|---|---|---|---|---|---|
Quarzglas | 100% | - | - | - | - | - | - | - | - | - | - | - | - | - |
Kalk-Natron-Glas | 72% | 2% | 14% | - | - | 10% | - | - | - | - | - | - | - | - |
Floatglas | 72% | 1,5% | 13,5% | - | 3,5% | 8,5% | - | - | - | - | - | - | - | - |
Bleikristallglas | 58% | - | 4% | 9% | - | - | 2% | 24% | - | - | - | - | - | - |
Laborglas | 80% | 3% | 4% | 0,5% | - | - | 12,5% | - | - | - | - | - | - | - |
E-Glas | 54% | 14% | - | - | 4,5% | 17,5% | 10% | - | - | - | - | - | - | - |
40% | 1,5% | 9% | 6% | 1% | - | 10% | 4% | 15% | 13% | - | - | - | - | |
Chalkogenidglas 1 | - | - | - | - | - | - | - | - | - | - | 12% | 55% | 33% | - |
Chalkogenidglas 2 | - | - | - | - | - | - | - | - | - | - | 13% | 32% | 30% | 25% |
Glas-Zuschlagstoffe sind unter anderem:
- andere Flussmittel zur Verminderung des Schmelzpunkts
- Zinkoxid
- Thallium
- zur Veränderung der Brechzahl
- Bariumoxid
- Bleioxid (absorbiert auch Strahlung)
- Cer wird für Glas verwendet, das Infrarotstrahlung absorbiert.
- Boroxid verändert als Zusatz die thermischen und elektrischen Eigenschaften.
- Aluminiumoxid erhöht die Bruchfestigkeit
- Trübungsmittel
- Zinndioxid
- Calciumphosphat
- Fluorid für Opalglas
- Zirkoniumdioxid
Übergang von der Schmelze zum festen Glas
Im Unterschied zur Abkühlung von kristallinen Materialien ist beim Glas der Übergang von der flüssigen Schmelze zum Feststoff ein allmählicher. Hier spricht man daher nicht von einem Schmelzpunkt sondern von einem Transformationsbereich. Im Laufe der Abkühlung nimmt die Viskosität des Materials stark zu. Dies ist das äußere Zeichen für eine zunehmende innere Struktur. Da diese Struktur kein regelmäßiges Muster aufweist, nennt man den Zustand der Schmelze im Transformationsbereich, wie auch des erstarrten Glases, amorph. Am kühlen Ende des Transformationsbereichs liegt ein thermodynamischer Übergang, der für Glas charakteristisch ist und daher den Namen Glasübergang trägt. An ihm wandelt sich die Schmelze in den festen, glasartigen Zustand, den das Glas auch bei weiterer Abkühlung zeigt. Der Glasübergang zeichnet sich durch eine sprunghafte Änderung des Wärmeausdehnungskoeffizienten sowie eine Abnahme der spezifischen Wärme Cp aus.
Diese Abfolge von Transformationsbereich und Glasübergang ist charakteristisch für alle Gläser, auch solchen, die aus Kohlenwasserstoffen bestehen. Der amorphe, viskose Zustand der Schmelze im Transformationsbereich wird für die Bearbeitung von Glas durch Glasblasen ausgenutzt. Er erlaubt eine beliebige Verformung, ohne dass Oberflächenspannung und Gravitation das Werkstück sofort zerfließen lassen.
Formgebung
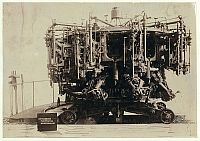
Je nach Produkt wird Glas unterschiedlich geformt. Dabei unterscheidet man vor allem Gläser, die gepresst, geblasen, gedüst, gesponnen oder gewalzt werden.
- Vergleiche: Glas - Formgebung
- Hohlglas wird in mehreren Verfahren durch Pressen, Blasen, Saugen und Kombinationen dieser Techniken hergestellt. Hier dominiert die IS-Maschine, die im Blas-Blas- oder Press-Blas-Verfahren arbeitet. Für höherwertige Tafelware kommen Press-Blas-Verfahren zum Einsatz, die karusellförmig arbeiten.
- Glasfasern werden durch Spinnen im so genannten TEL-Verfahren produziert.
- Flachglas wird im Floatverfahren hergestellt, gezogen, gewalzt oder gegossen
- Rohrglas wird seit 1912 durch kontinuierliche Ziehverfahren hergestellt
Kühlung
Entspannungskühlen
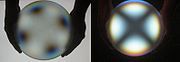
In jedem Glasgegenstand entstehen bei der Formgebung mechanische Spannungen als Folge von Dehnungsunterschieden im Material. Diese Spannungen lassen sich mit optischen Spannungsprüfern messen (Spannungsdoppelbrechung). Die Spannungsanfälligkeit hängt vom Ausdehnungskoeffizienten des jeweiligen Glases ab und muss thermisch ausgeglichen werden.
Für jedes Glas lässt sich zwischen der oberen Kühltemperatur (Viskosität von 1013 mPa s) und einer unteren Kühltemperatur (1018 mPa · s), in der Regel zwischen 550° C und 350° C, ein Kühlbereich festlegen. Die Spannungen verringert man durch definiertes langsames Abkühlen im Kühlbereich, dem Tempern.
Die Zeit, in der ein Glasgegenstand den Kühlbereich durchlaufen kann, ist maßgeblich von der je nach Glasart zu überbrückenden Temperatur, der Stärke (Dicke) des Gegenstands abhängig. Im Hohlglasbereich sind dieses zwischen 30 min und 100 min, bei großen optischen Bauteilen kann eine langsame Abkühlung mehreren Wochen und Monaten notwendig sein, um Spannungen und somit Bildverzeichnungen zu vermeiden.
Die kontrollierte Temperatursenkung kann mit unterschiedlichen Öfen vorgenommen werden. Man unterscheidet periodische Kühlöfen und kontinuierliche Kühlbahnen. Kühlöfen eignen sich nur für Sonderfertigungen und Kleinstchargen, da nach jeder Entnahme der Werkstücke der Ofen wieder auf Temperatur gebracht werden muss. Industriell werden Kühlbahnen genutzt. Hier wird die Produktion auf Stahlmatten (Hohlglas) bzw. Rollen (Flachglas) langsam durch abgestuft geheizte Ofensegmente transportiert.
Oberflächen-Veredelung
- Durch chemische und/oder physikalische Gasphasenabscheidung können feinste Metallbeschichtungen aufgebracht werden. Die meisten Fenster- und Autogläser werden auf diese Weise mit für Infrarotlicht undurchlässigen Beschichtungen versehen. Die Wärmestrahlung wird reflektiert und Innenräume heizen durch Sonneneinstrahlung weniger auf. Gleichzeitig werden die Wärmeverluste im Winter reduziert, ohne dabei die Durchsichtigkeit wesentlich zu beeinträchtigen.
- Die Beschichtung mit dielektrischem Material, das selbst durchsichtig ist, aber ein vom Glasträger abweichende Brechzahl aufweist, sind sowohl Verspiegelungen als auch Entspiegelung möglich. Dies wird bei der Herstellung von Brillengläsern und Linsen für Fotoapparate eingesetzt, um störende Reflexionen zu vermindern. Für wissenschaftliche Zwecke werden Schichten hergestellt, die mehr als 99,9999% des einfallenden Lichts einer bestimmten Wellenlänge reflektieren. Umgekehrt kann auch erreicht werden, dass 99,999% des Lichts die Oberfläche passieren.
- Durch Sandstrahlen oder mit Flusssäure kann die Oberfläche so weit aufgeraut werden, dass das Licht stark gestreut wird. Es erscheint dann milchig und nicht mehr durchsichtig, jedoch wird weiterhin nur sehr wenig Licht absorbiert. Daher wird diese Technik häufig für Lampenschirme, oder für blickdichte Fenster angewandt.

© biancahoegel.de;
Datum der letzten Änderung : Jena, den: 03.04. 2022